What is HONEYCOMB
SANDWICH PANEL
A sandwich panel (or sandwich structure) is an element consisting of two resistant layers, called skins or faces, separated by a connective material called core.
The core is typically lightweight and resistant material, whose only function is to distance the skins, in noble material and with reduced thickness.
The axial stiffness of the core is absolutely negligible compared to that of the skins, which are responsible for the loads on the surface.
The presence of the core is instead useful to increase the value of the flexural stiffness of the panel, which depends on the distance of the sheets from the middle surface.
The use of this structure is therefore comparable to the concept of the "double T beam", where the core serves to increase the flexural stiffness in the direction of same.
By distancing the skins, you get a remarkable increase in stiffness compared to a panel consisting only of a material thickness equal to that of the two sides with a greatly reduced weight increase.
For these reasons, sandwich panels have become increasingly popular in the aerospace industry over the past forty years.
A more common example of a sandwich panel is one made of cardboard in which the flat outer layers are separated by a layer of corrugated cardboard.
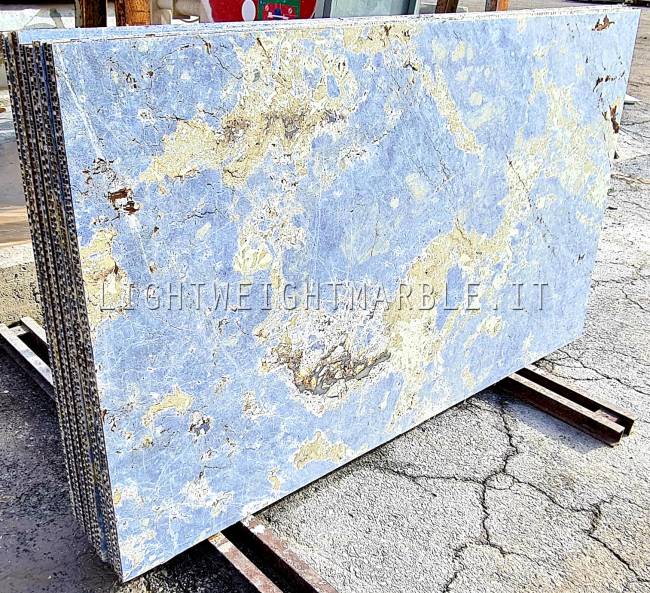
Lighweight granite - Producied by FFPANELS®
SKINS
The skins are usually made of material with high mechanical strength, which can be a composite material made of fibreglass, carbon or Kevlar, or even thin aluminium or steel.
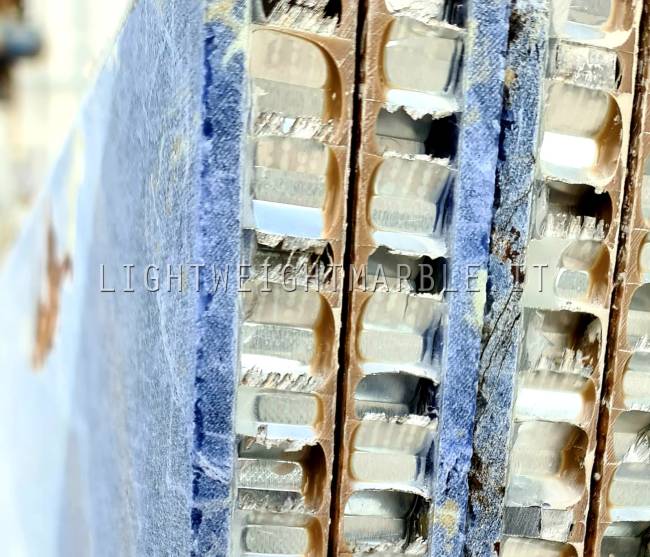
Lighweight granite - Producied by FFPANELS®
CORE
The core involves use of structures with honeycomb cells, simply called honeycomb, (or alternative foams).
Honeycomb cells are obtained in various ways:
In the second case, the slabs are first worked by deforming them plastically through the passage between toothed rollers with appropriate geometries and the finished product is obtained by bonding.
|*Honeycomb structures consisting of aramid fibre cells in a thermosetting resin matrix.
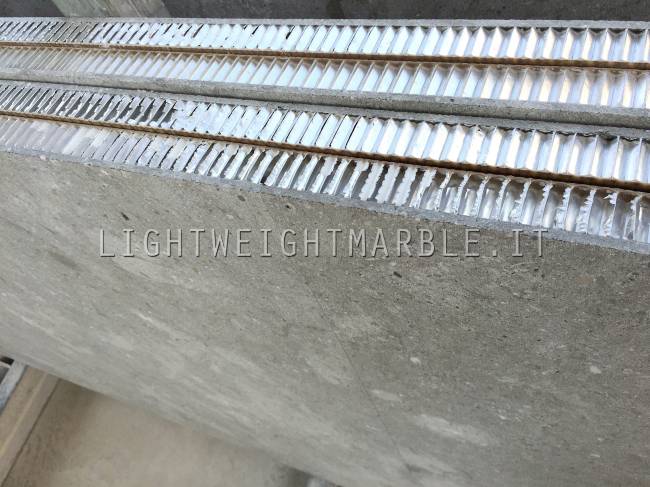
Lighweight marble - Producied by FFPANELS®
You are reminded of some local or global instability issues that have honeycomb core sandwiches panels:
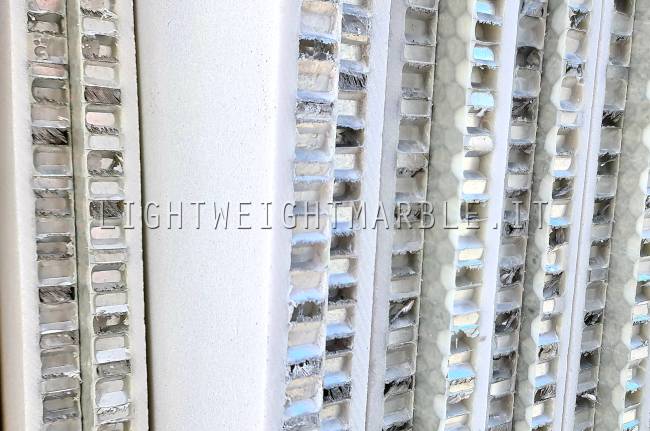
Lighweight marble - Producied by FFPANELS®
Foams are defined as those cellular materials obtained by dispersing a gas into a solid plastic material.
The foam can be:
The foam can be in liquid state, if it is pressed into the mould together with the gas, or in semi-finished solid blocks that are appropriately cut and processed.
Foam is easily processed and is low cost, and for this reason it is usually used to build sandwich panels, despite its mechanical characteristics being inferior to those of honeycomb.
It offers excellent thermal and acoustic insulation, excellent vibration damping and shock resistance.
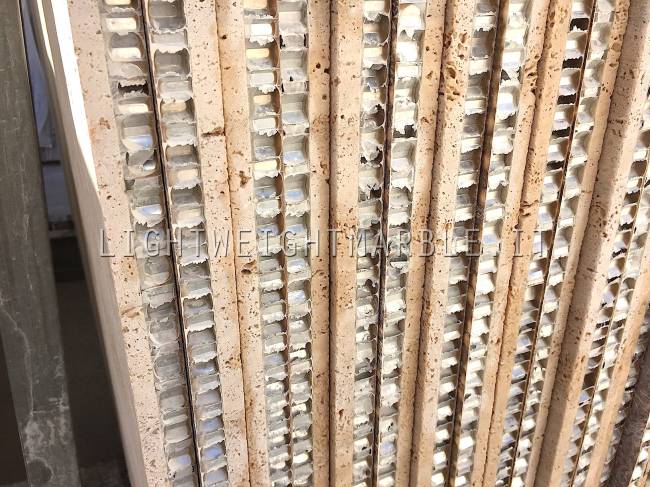
Lighweight marble - Producied by FFPANELS®
STRUCTURAL ADHESIVE
The adhesive is necessary to join the skins to the core. Film adhesives are used with characteristics very similar to those of the resins that make up the matrixes in composite materials, therefore curing is necessary in autoclave. There are different chemical formulations depending on the nature of the materials to be joined (metal-metal, metal-composite, composite-composite).
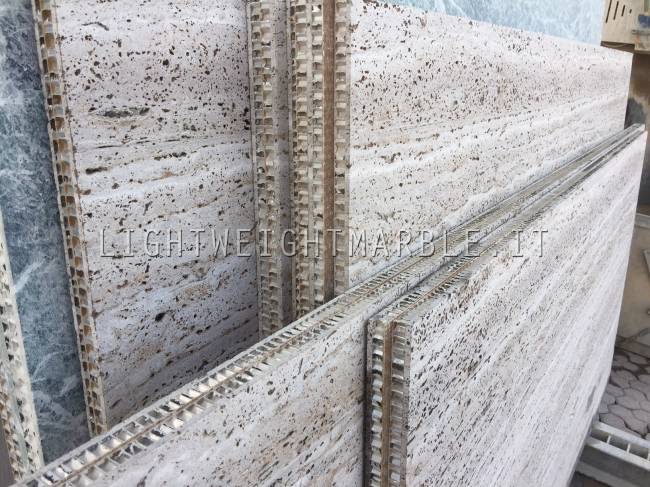
Lighweight marble - Producied by FFPANELS®
INTERESTING FACT
The new Airbus A380 uses a new type of honeycomb made of Kevlar, which is used for applications such as the interior panels and wing flaps.
Of equal weight, Kevlar is five times stronger than steel and its use allows substantial weight savings.